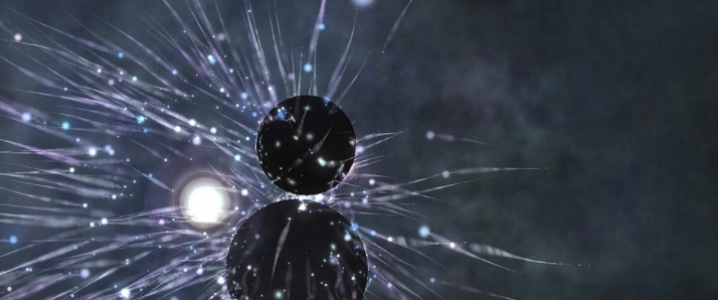
Augmented reality and virtual reality technology is expanding beyond gaming and beyond chasing and catching Pokemon. Now, it’s hit the oil industry and aims to save it money.
The oil and gas industry has started using AR to fix and maintain equipment at oil and gas facilities, cutting downtime and costs and saving on travel expenses for flying specialized staff thousands of miles to the actual facilities.
AR headsets with smart goggles provide on-site technicians with wireless connection directly to headquarters staff or to the most skilled experts thousands of miles away, who can guide the on-site staff through the tasks they perform via audio and video.
Analysts expect technological advances to play an increasingly important part in the continued cost cuts for oil—an industry that has already slashed costs across the board to survive and reposition itself to profit at low oil prices.
The AR revenue for the energy and utilities sector will be a US$18-billion market in 2022, with platform and licensing, as well as smart glasses hardware, comprising the majority of that market, according to ABI Research.
This year alone, the energy and utilities industries will account for 17 percent of global smart glasses shipments, the advisory firm said.
“AR enables better visualization of underground assets, pipelines in concrete, or complex components, which help avoid breaks while digging, detect dangerous leaks, and reduce accidents. Accordingly, employee safety will be maintained along with a decline in errors and total downtime,” Marina Lu, Senior Analyst at ABI Research, says.
For an oil industry recovering from the oil price crash, cutting downtime and costs and boosting efficiency is the new normal at oil prices half their level compared to 2014.
So, companies have jumped on the ‘digital disruption’ bandwagon and some are already using smart goggles and wearables to reduce downtime and increase safety.
For example, Baker Hughes, now part of GE, has been using the Smart Helmet developed by Italian company VRMedia Srl.
Recently, Baker Hughes has replaced parts of a turbine at a petrochemical plant in Malaysia in five days and no travel expenses as one on-site technician was guided by specialized U.S. engineers supervising the work remotely from a Baker Hughes site in California. The replacement of the parts would have otherwise involved at least 10 days of halted operations at the plant and US$50,000 to fly the American team, Bloomberg reports.
Cutting the downtime saves millions of dollars to oil companies.
According to Deloitte, a 100,000-bpd refinery losing a single day of operations could reduce revenues by more than US$5.5 million and cut profit by US$1.4 million.
Oil and gas facilities shut for 27 days each year on average, Bloomberg quoted industry analyst Kimberlite International Oilfield Research as saying.
Remote AR is not the cure-all wonder tech because it needs reliable wireless networks which oil rigs in the wilderness often lack, and because headsets need to meet strict safety standards to be used close to hazardous materials.
But some of the biggest oil firms are already using some kind of AR or VR or wearables to increase safety and efficiency and cut costs.
Eni and MIT have created wearables to improve workplace safety in the oil and gas industry.
Shell is using VR in training for safety training procedures at a deepwater oil project offshore Malaysia.
BP uses AR smart glasses in its U.S. operations, alongside drones and advanced analytics.
Scotland-based Cyberhawk performs inspections and surveys with drones at oil and gas platforms, plants, and refineries across the world, and its clients include major oil and gas companies.
The use of sophisticated and smart technologies is spreading across the oil sector, in which the biggest firms and all those smaller companies who survived the downturn continue to look to save more costs.